Seamless Chimney Design Claims vs Reality
Seamless Chimney Design Claims vs Reality - Defining the allure of seamless design claims
"Defining the allure of seamless design claims" unpacks the persuasive power inherent in marketing and communicating designs as entirely smooth and continuous. This explores the fascination with the notion that complexity has been completely resolved, leaving no visible junctures or transitions. It prompts an examination of why this presentation holds such appeal and encourages looking closer at what assumptions underpin the declaration of invisibility in design applications.
The perception of uninterrupted surfaces seems to require less mental effort for the brain to process visually. This apparent reduction in processing friction contributes positively to how aesthetically pleasing or desirable something is perceived to be at a basic level.
There's a theory that our biological wiring might favor smooth, unbroken forms. This could stem from an ancient link associating such surfaces with indicators of health, structural soundness, or resilience against damage. This potential subconscious connection lends seamless designs a sense of inherent quality or durability.
Visual experiences of seamlessness can trigger surprising links to tactile sensations. Seeing a smooth, continuous surface might subconsciously bring to mind the feeling of polished material or still liquid, contributing a layer of comfort or quality perception that crosses sensory boundaries.
Achieving genuinely seamless results often implies advanced manufacturing processes and high levels of precision. As such, the very claim of seamlessness functions as a powerful, albeit sometimes implicit, signal of technical sophistication and, consequently, potential exclusivity or expense. This perception of elevated craft and cost feeds into its desirability, particularly when design serves as a status marker.
Beyond mere looks, an unbroken design form intuitively suggests superior functional performance. It implies fewer potential points of weakness, seemingly reducing risks like water penetration, thermal bridging, or structural discontinuities at joints. This creates a cognitive expectation of durability and robustness, an implicit promise of reliable long-term performance, which significantly adds to its appeal, even if not always guaranteed in practice.
Seamless Chimney Design Claims vs Reality - The engineering complexities behind a working chimney
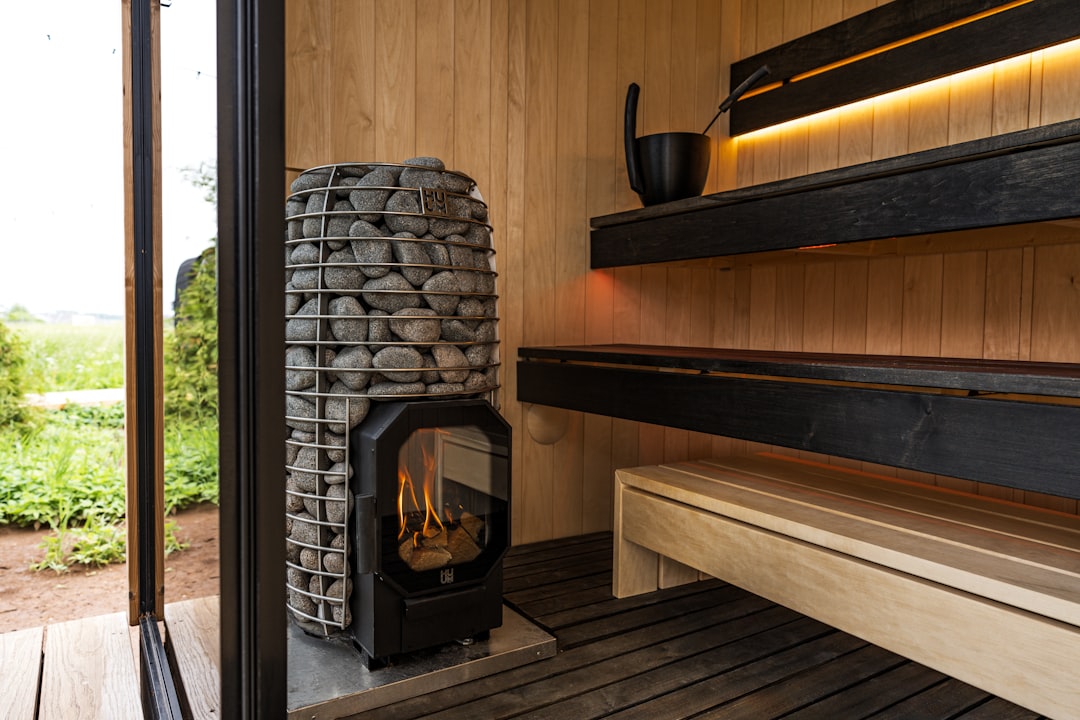
Designing a functional chimney is a demanding engineering exercise that must successfully integrate several complex requirements. It fundamentally involves managing the high-temperature, potentially corrosive byproducts of combustion and safely releasing them at a height sufficient to disperse pollutants, all while ensuring the structure itself can withstand environmental assaults and operational stresses over a long lifespan.
Calculating the appropriate dimensions, particularly the diameter, is critical. This isn't simply about aesthetics; it must accommodate the specific volume and flow rate of the gases being moved. This sizing directly impacts the vital function of draft – the natural upward movement of gases driven by buoyancy, which must be carefully balanced against frictional losses within the flue. Getting this wrong compromises the system's ability to evacuate exhaust effectively.
Structural considerations are equally complex. Beyond supporting its own weight, the chimney stack is subjected to immense external forces. Wind loading is a primary concern, requiring analysis of potential vortex shedding and other complex aerodynamic effects, which vary significantly based on the chimney's shape. Seismic activity adds another layer of dynamic stress that the design must account for, as do temperature fluctuations between operation and downtime, which cause expansion and contraction.
Material selection and protection are non-trivial. The inner surfaces face relentless exposure to heat, moisture, and corrosive chemicals. This necessitates specialized internal linings, such as refractory materials or corrosion-resistant alloys, distinct from the main structural shell, acting as a sacrificial or protective layer essential for durability.
Critically, while some design portrayals might suggest standalone, perfectly independent structures, the engineering reality is often more integrated. Chimneys must interface with the buildings or systems they serve, and this connection often introduces structural dependencies and additional load paths not always apparent in simplified representations. Designing for these real-world interface conditions, thermal bridges, and accumulated stresses at connection points adds significant complexity and can challenge notions of complete structural autonomy.
Ultimately, a reliable working chimney is the result of rigorous analysis, careful material specification, and detailed structural design that acknowledges and accounts for a multitude of interacting physical phenomena and external forces, rather than relying on simplified ideals.
Delving into the tangible mechanics of a chimney reveals a fascinating intersection of fluid dynamics, thermodynamics, chemistry, and structural considerations, often more complex than superficially 'seamless' depictions might suggest. From a researcher's standpoint, observing a functional chimney involves appreciating these subtle yet critical interactions:
The dynamic interaction of wind with the chimney structure is far more intricate than simple force. High winds flowing across the chimney's peak induce fascinating aerodynamic effects, sometimes creating suction that surprisingly aids the 'draft', but turbulence is a constant concern, frequently causing chaotic flow patterns or undesirable backflows into the building. It's a delicate balance, constantly shifting with external conditions.
Combusting fuel releases a cocktail of gases, including significant amounts of water vapour and other chemical species. As these hot gases cool against the flue walls, this vapour condenses, forming corrosive solutions – think dilute acids – that relentlessly attack and degrade materials like traditional brick mortar and even certain metallic liners over time. It's a slow, chemical battle occurring within the flue.
It's not just the chimney itself; the adjacent building and even nearby structures profoundly influence local airflow. The intricate shapes of roofs and surrounding massing can generate localized areas of lower pressure right where the smoke needs to exit, essentially creating an aerodynamic 'dam' that actively hinders the necessary upward movement of combustion byproducts. Site context and surrounding geometry are critical, often underestimated factors.
The liner material operates under extreme duress. It's subjected to punishing thermal cycling – from cold ambient conditions potentially skyrocketing past 1000°C during operation or a worst-case scenario chimney fire. Simultaneously, it must fend off the corrosive chemical onslaught from condensed flue gases mentioned earlier. Finding materials capable of handling *both* simultaneously and durably is a significant materials science challenge that doesn't always have a simple answer.
One persistent issue is creosote, that nasty, flammable residue. It precipitates out from the flue gases when volatile organic compounds within them cool sufficiently to condense. This accumulation, a major fire risk, is highly sensitive to system parameters: the temperature profile along the flue, the type of fuel burned, and the consistency of the airflow (or 'draft'). Managing this requires careful control over system design and operation, acknowledging the inherent complexities of combustion product behaviour.
Seamless Chimney Design Claims vs Reality - Common issues encountered despite design aspirations
Achieving the seemingly effortless performance implied by design aspirations often confronts persistent real-world issues. Despite careful planning, practical chimney systems face challenges that compromise the ideal. Airflow dynamics are difficult to perfect; slight mismatches in sizing or external influences can easily disrupt draft, leading to poor function or backdrafting. Structural robustness is continually tested by environmental forces, revealing unforeseen weaknesses over time. Furthermore, internal materials endure relentless attack from heat and combustion byproducts, demanding ongoing upkeep often overlooked in practice. These practical realities underscore that the aspiration for a seamlessly performing system is constantly challenged by inherent engineering and maintenance demands.
Even components meticulously crafted for a uniform appearance harbor subtle inconsistencies at the microscopic level. Temperature shifts inherent in a chimney's operational cycle, fluctuating between ambient and high heat, readily exploit these variances. Discrepancies in thermal expansion rates within ostensibly homogeneous materials or across chemically bonded layers generate localized internal stresses. Over extended periods, this can quietly initiate microscopic fractures, frustrating the ideal of a perfectly stable structure.
Beneath the surface, the variability of soil conditions presents another challenge that confounds simple design ideals; absolute uniformity is rarely encountered in reality. Consequently, the substantial, concentrated load of a chimney structure can induce differential, though potentially minute, settlement relative to adjacent building elements that bear lighter loads. This uneven settling introduces complex, unforeseen structural stresses and torsional forces at the critical interface points where the chimney integrates with the main structure, challenging the assumptions of load distribution underpinning a 'seamless' connection.
Despite rigorous efforts aimed at achieving airtightness, microscopic discontinuities are virtually inevitable. These pathways arise from myriad sources – molecular bond lines that aren't perfectly continuous, or imperfections stemming from material curing processes. Such tiny routes allow unintended, 'parasitic' air movement into or out of the flue. This subtle ingress or egress disrupts the delicate, carefully designed pressure gradients and gas flow dynamics, leading to performance degradation, such as compromised draft consistency, in ways that are visually undetectable from the exterior.
Examining material interfaces at the atomic scale reveals that even outwardly fused or continuous junctures aren't truly monolithic entities. They typically consist of distinct chemical bonds between different elements or incorporate residual trace materials from manufacturing. Over significant durations, slow-acting chemical processes can unfold across these microscopic boundaries. Phenomena like galvanic corrosion, driven by electrochemical potential differences, or the subtle leaching of specific elements can quietly erode structural integrity or trigger localized material breakdown, undermining the long-term resilience implied by a seamless aesthetic.
Any substantial structure, a chimney included, possesses inherent natural frequencies at which it is predisposed to vibrate. Even seemingly innocuous environmental forces like steady airflow across the stack or minor, non-damaging ground tremors can inadvertently align with and excite these frequencies. This resonant response induces subtle, continuous oscillatory motion within the structure. While this movement is often imperceptible visually, this persistent, cyclic stressing generates material fatigue over time, capable of initiating or propagating micro-cracks in ways not typically captured or accounted for in simplified, static design models prioritizing a seamless outcome.
Seamless Chimney Design Claims vs Reality - Ongoing reality of maintaining chimney performance
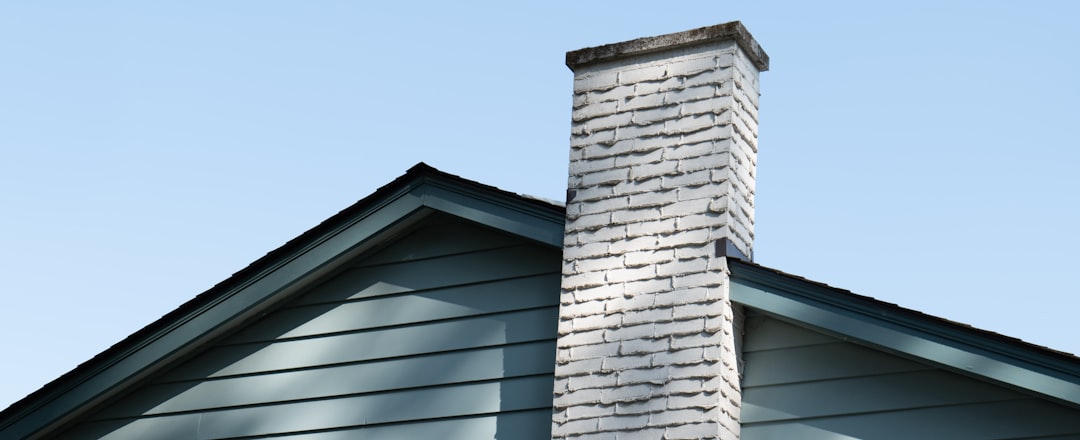
The practical truth of keeping a chimney performing well is an ongoing challenge that extends well past the initial planning and building stages. Maintaining a chimney isn't merely about occasional fixes; it is fundamentally necessary for guaranteeing both safe operation and energy efficiency. This is because chimneys are constantly battling against the intense chemical reactions and temperature swings occurring internally, as well as enduring environmental pressures externally. The subtle yet complex dynamics of airflow and the gradual breakdown of materials over time mean that even systems initially put together with great care can develop issues if they aren't regularly looked after. The reality is that the intricacies of how a structure interacts with its surroundings and the long-term effects on its integrity create performance challenges that often go unnoticed until a problem arises. Ultimately, the appealing notion of a perpetually effortless or 'seamless' system runs directly counter to the practical need for consistent inspection and care to ensure a chimney continues to function correctly and safely over its lifespan.
The journey from design ideals to operational reality reveals that maintaining chimney function involves managing persistent, subtle challenges.
Despite diligent cleaning efforts, microscopic residues – whether chemically bound creosote remnants or residual compounds from the combustion process itself – can embed themselves within porous flue materials. These persistent traces may continue contributing to slow, ongoing material degradation or represent a subtle, difficult-to-fully-eliminate low-level fire ignition risk over time.
Often, external moisture ingress presents a more significant long-term threat to structural integrity than the moisture generated by combustion inside the flue. Water seeping in from rain or through faulty flashing around the chimney's exterior penetrates masonry and supports. Subject to freeze-thaw cycles, this water causes cumulative expansion and contraction, slowly but surely eroding mortar and weakening the overall structure, sometimes more profoundly than internal chemical attack.
Current standard inspection methods, including visual checks and internal camera surveys, possess inherent limitations. They frequently fail to detect subtle material fatigue or the initial stages of micro-cracking. This damage can be quietly developing deep within the flue liner systems, initiated by the relentless stress of thermal cycling (from cold to high heat and back) or constant, subtle vibration induced by wind resonance over the chimney's lifespan.
In contemporary, well-sealed buildings, the absence of a dedicated external air supply for combustion can create a critical deficiency. When the appliance is starved for air, the fire burns less efficiently, resulting in lower flue gas temperatures and reduced velocity. This cooler, slower exhaust stream scientifically promotes increased creosote condensation along the cooler interior flue walls, compounding risk, somewhat ironically, due to the building's improved airtightness elsewhere.
The soot and other particulate matter deposited on internal flue surfaces are not merely inert substances. These layers often contain chemically active components. Microscopically, these particles can act as catalysts, accelerating slow-acting chemical breakdown and facilitating the corrosion of liner materials, particularly during the periods *between* heating cycles when temperatures are lower and condensation may persist, allowing chemical reactions to proceed unchecked.
More Posts from archparse.com: