Concrete Construction Self Perform Versus Subcontract Evaluating Efficiency
Concrete Construction Self Perform Versus Subcontract Evaluating Efficiency - Calculating internal capacity for concrete pours
Precisely assessing the internal capacity for handling concrete pours is a fundamental consideration for construction firms evaluating whether to perform the work with their own forces or contract it out. This isn't merely a count of available personnel or equipment; it involves a realistic evaluation of how your team, tools, and material logistics can effectively manage the demands of a specific pour. Grasping this true capability is vital for intelligent planning and resource deployment, which directly impacts operational efficiency and project schedules. Misjudging this internal strength can lead to wasted resources, delays, or failing to capitalize on opportunities where self-performing concrete work might offer distinct advantages in control, execution speed, and safety compared to relying on external parties.
The hydrostatic pressure generated by fresh concrete is a force that can, perhaps surprisingly, induce subtle outward deflections in even seemingly rigid formwork systems. This means the internal volume receiving concrete is not perfectly static or identical to the initial geometric design, becoming slightly larger under load. Consequently, accurately predicting the precise volume required demands consideration beyond simple dimensional geometry.
The volume occupied by air voids within the concrete mix – both deliberately entrained air for durability and unintentionally entrapped air from handling – constitutes a portion of the total volume that fills the formwork. This air content isn't always perfectly uniform throughout a pour, influenced by mixing, transport, placement techniques, and concrete properties, introducing variability into the calculation of the *actual* solid concrete volume within the given capacity.
How the various aggregate sizes within the concrete mix pack together influences the final bulk volume of the hardened material. Unlike simply summing the volumes of individual components, the complex interplay of aggregate shape, size distribution, and the paste volume dictates the density and final occupied space. This means the theoretical volume calculated from batch quantities might not precisely match the volume achieved *in situ*, impacting total capacity estimates.
Variations in concrete slump or flow characteristics, often influenced by temperature, admixtures, or even just placement time, significantly affect how completely and easily the mix can flow into and fill complex internal formwork geometries around reinforcement or blockouts. The resulting 'effectively' filled volume might differ from the rigid formwork volume if the concrete doesn't achieve full consolidation in all areas, posing a challenge for accurate capacity assessment.
While necessary for consolidation and defect reduction, vibration can inadvertently remove intentionally entrained air if overdone or improperly applied. This loss of desirable air decreases the overall volume occupied by the concrete within the formwork, potentially requiring marginally more material than initially estimated based on theoretical calculations for the specified form capacity to reach the target elevation.
Concrete Construction Self Perform Versus Subcontract Evaluating Efficiency - Balancing project demands against in-house teams
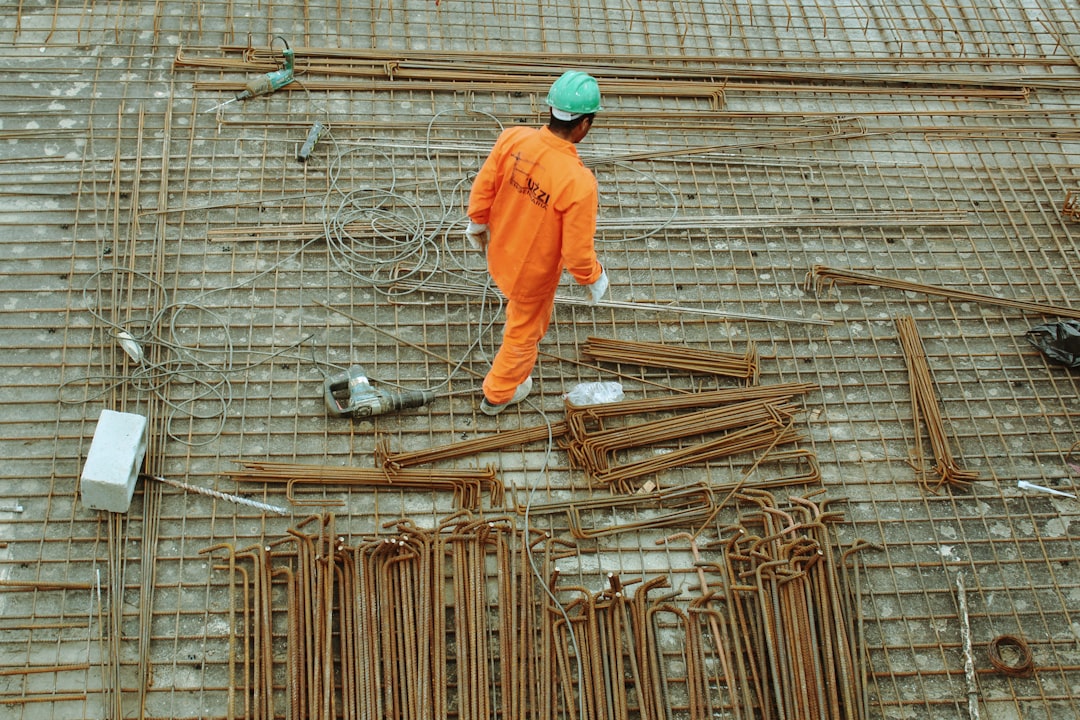
Navigating how to fulfill project requirements using internal staff instead of bringing in outside help is a constant balancing act for construction firms. It requires more than just a basic headcount; a genuine assessment of whether the in-house team truly possesses the necessary expertise, availability, and supporting resources to handle the job's specifics is crucial. Companies must honestly weigh the direct and indirect costs associated with self-performing against subcontracting, factoring in the demands on existing management and project oversight capabilities. A mismatch between project complexity or scale and the realistic capacity or skill set of the internal crew can predictably result in operational friction, cost overruns, and setbacks to the schedule. The decision to keep work in-house versus subcontracting should ultimately stem from a rigorous, objective evaluation aimed at achieving overall project success and long-term efficiency, rather than defaulting to one approach.
Managing internal resources against fluctuating project needs in concrete construction presents complexities beyond simply counting available hands or calculating raw capacity. Consider these less intuitive aspects of balancing project demands with in-house teams:
1. Pushing an internal concrete crew with relentless project schedules can lead to more than just physical exhaustion; it imposes a substantial cognitive burden. Studies have shown that this chronic mental load can impair judgement and increase the likelihood of fundamental errors in critical tasks, from mix design checks to complex formwork adjustments.
2. An in-house team's specialized expertise in areas like high-strength mixes, post-tensioning anchorages, or intricate architectural concrete finishes isn't static. Without consistent, demanding projects requiring these specific skills, that hard-won proficiency can erode, potentially resulting in slower execution, diminished quality, or a greater need for re-training when such capabilities are eventually needed.
3. While intuitively more personnel might seem to equate to greater productivity, research into team dynamics suggests there are points where adding individuals to a specific concrete task can paradoxically decrease overall efficiency per person. This often stems from the exponential increase in necessary communication channels and the added complexity of coordinating actions within the larger group.
4. Regularly shifting concrete team members between entirely different project phases or types of work incurs a quantifiable cognitive cost often referred to as a "switching cost." The mental effort required to disengage from one task mindset and fully orient to the requirements of another can cause a temporary, but measurable, dip in focus and output efficiency upon starting the new assignment.
5. Highly experienced, stable in-house teams develop a form of collective, implicit knowledge – a deep, almost instinctive understanding of how materials will behave under specific site conditions, or an intuitive grasp of their teammates' strengths and weaknesses. This vital operational insight is accumulated through shared time and experience and is inherently difficult, if not impossible, to replicate or quickly transfer to a newly assembled or subcontracted crew.
Concrete Construction Self Perform Versus Subcontract Evaluating Efficiency - Considering external costs and specialized skills
Evaluating whether to handle concrete construction work in-house or bring in a specialist subcontractor increasingly demands a sophisticated assessment that moves beyond merely comparing upfront bids against internal labor costs. The evolving understanding highlights the critical need to rigorously weigh the often complex tapestry of external financial outlays alongside a granular analysis of the truly specialized skills required for the specific task. This integrated approach recognizes that the visible cost of a subcontractor is only one piece; the subtle costs of managing that external party, ensuring their quality meets standards, and the long-term strategic impact of not developing or maintaining those specialized skills internally, are becoming focal points in informed decision-making. The emphasis is now on a more critical, holistic appraisal of both the direct price tag of external help and the nuanced challenge of acquiring, overseeing, and benefiting from specialized expertise provided by others.
Beyond merely evaluating internal capacity and the current strain on existing teams, the decision between performing concrete work with one's own forces or engaging external specialists necessitates a critical examination of costs that reside outside the direct labor and material expenditure. This layer of external economic and risk factors often presents subtle yet significant influences on overall project efficiency and financial outcomes, sometimes challenging initial assumptions about the 'cheaper' approach.
The sheer administrative overhead involved in managing subcontractors – encompassing everything from the initial pre-qualification and vetting process through negotiating contract terms, overseeing daily quality control, tracking progress payments, and finally handling closeout paperwork – constitutes a tangible cost. Research suggests this management burden isn't negligible, potentially adding a percentage equivalent to 5-10% or even more on top of the subcontractor's quoted price, a cost often spread across general conditions but undeniably linked to the subcontracting model and frequently underestimated when compared purely on a unit price basis.
Taking on the execution of concrete placement, especially complex or high-risk elements like large structural pours or elevated decks, inherently shifts certain liabilities onto the self-performing firm. This increased exposure to potential site accidents, material failures, or construction defects directly translates into higher premiums for general liability and workers' compensation insurance policies compared to a business model that primarily subcontracts these riskier activities, effectively externalizing that operational risk premium.
When a project demands highly specific concrete expertise – perhaps requiring intricate formwork for architectural finishes, complex pumping logistics for extremely tall structures, or specialized knowledge for handling unique concrete mixes like high-strength or self-consolidating concrete – the market cost for securing such capabilities often carries a substantial premium. This isn't just paying for a person's time; it reflects the significant capital investment in specialized equipment, the years of accumulated knowledge, and the relative scarcity of truly proficient teams possessing these niche skills, making subcontracting these specific tasks potentially expensive but sometimes the only viable option.
Interestingly, companies specializing solely in concrete construction services frequently demonstrate a greater propensity, and perhaps necessity, to invest in and leverage advanced construction technologies tailored to their craft. This includes sophisticated parametric modeling for designing complex formwork, integrating real-time concrete temperature and strength monitoring systems, or employing advanced logistics software for concrete deliveries. By specializing, they can amortize the high cost of these cutting-edge tools across a larger volume of specific concrete projects than a general contractor might, potentially offering technological efficiencies not easily replicated in-house without significant dedicated investment.
Finally, transferring the responsibility for executing concrete work to an external entity, the subcontractor, often requires securing performance and payment bonds. These financial instruments, guaranteeing the subcontractor completes the work as specified and pays their own suppliers and labor, introduce a direct, calculable cost, typically hovering around 1% to 3% of the subcontract sum. This bonding expense is essentially a fee paid to a third party for assuming a portion of the project's execution and financial risk that would otherwise reside internally with the self-performing firm.
Concrete Construction Self Perform Versus Subcontract Evaluating Efficiency - Tracking schedule impact on concrete phases
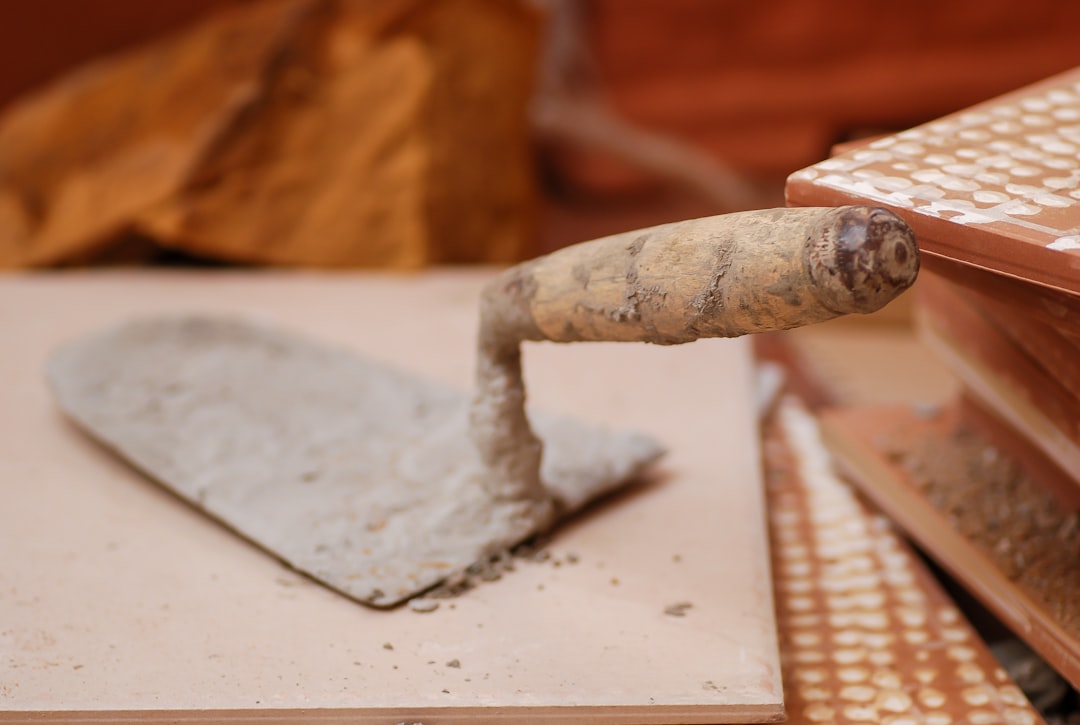
Managing the impact of concrete phases on the project schedule is fundamental to effective construction execution. The speed and efficiency of concrete operations directly influence whether overall timelines are met, particularly as construction schedules are often compressed. Handling concrete work internally *can* offer a more direct hand in controlling the pace, potentially mitigating delays sometimes seen when relying on outside parties whose availability or priorities may differ. However, successfully self-performing these critical tasks requires diligent tracking and management of labor, materials, and site coordination; failure to closely monitor the interplay of these elements can certainly lead to internal hold-ups. Ultimately, maintaining clear visibility into the schedule of concrete activities and how they integrate with the larger project timeline remains critical for navigating complex construction processes effectively.
Tracking the impact on schedule within concrete construction phases reveals subtle factors beyond just pour volume and crew size. For instance, the rate at which concrete gains strength isn't a simple function of time; tiny variations in ambient and mix temperatures dramatically alter hydration kinetics, causing non-linear shifts in set times and strength development. Failure to monitor this precisely means planned milestones, like formwork release or when subsequent structural loads can be applied, could be missed, sometimes significantly impacting the project's critical path. Furthermore, the surrounding relative humidity, often overlooked, profoundly influences surface evaporation from the fresh mix, dictating crucial initial set times for finishing operations and potentially affecting long-term durability if curing isn't managed, creating schedule risks at different stages. Modern approaches are increasingly moving away from fixed calendar waits post-pour; instead, verifying actual achieved concrete strength using embedded maturity sensors allows for data-driven decisions on when it's safe to proceed with follow-on activities, directly accelerating or delaying the critical path based on empirical performance, although integrating this technology isn't universally practiced or straightforward. The chemical complexity of admixtures, particularly retarders and accelerators used for controlling set times, can introduce unexpected synergistic or antagonistic interactions under site conditions that deviate from theoretical predictions; rigorous field tracking is necessary to avoid unforeseen delays or undesirable rapid stiffening that disrupts planned workflows. Lastly, adopting different material types, like Self-Consolidating Concrete (SCC), fundamentally alters the placing process and required monitoring parameters. While potentially more expensive initially, the speed and ease of placement can dramatically shorten the duration of the concrete phase, enabling earlier access for other trades and offering a potential overall schedule acceleration, but this relies on tracking flow and stability rather than just traditional slump.
More Posts from archparse.com: